STARK Forced Ventilation
We Make Motors Cool

Overheating: one of the most common causes of motor failure
Heat is the biggest enemy of electric motors. According to the International Electrotechnical Commission (IEC) and National Electrical Manufacturers Association (NEMA), operating a motor just 10°C above its recommended maximum operating temperature cuts its life in half, even if the overheating was only temporary.
As manufacturer in the industry the last thing you want to occur is downtime or breakdown because of an overheated motor. When overheating destroys a motor, lost revenues may exceed the costs of replacement purchase and installation. A ruined batch or stopped assembly line can delay a production and cause customers to seek out another supplier.
That’s never good for business, and it’s probably not something you want to be known for by potential customers.
In the following situations we advise to use forced ventilation:
- High torque on low speed
- Operation of a motor with frequency inverter with a setting range > 1:20
- Frequency inverters that have to generate rated torque at low speeds or even at standstill
- Use of an encoder system on the B-side (when the integrated fan is removed)
- Drives with high starting frequency
- Drives that are operated above the rated speed (high fan noise)
To prevent motors from overheating cooling is necessary to continuously transfer the heat to a cooling medium, such as the air. IEC and NEMA state that for every 10°C that the motor is cooler, the insulation life will be doubled. This can be achieved with forced ventilation.
Forced ventilation units are separately driven fans for electric motors. An IC 416 (formerly IC43) externally cooled motor can operate at a higher load and is likely to have a longer life than an electric motor without forced ventilation.
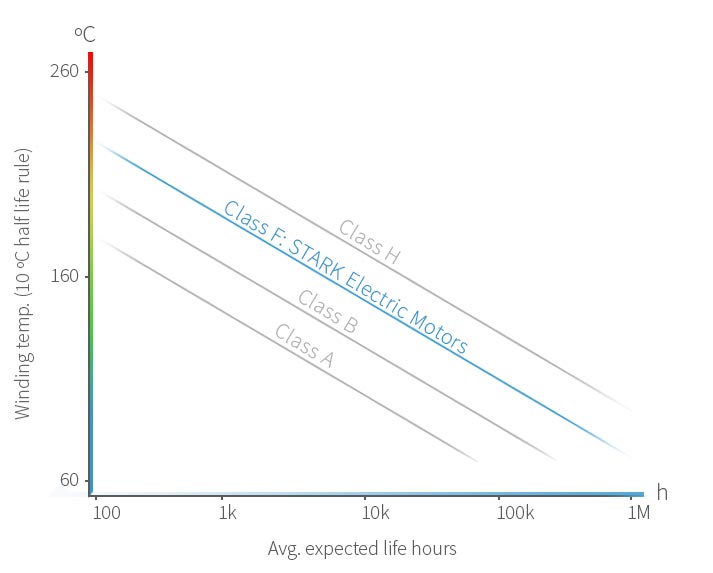
Contact us and learn more
Superior External Cooling with STARK Forced Ventilation
STARK forced ventilated motor units (IC 416) are engineered in Europe and with cooling running axially they keep the air flow close to the surface of the motor along its entire length, thus improving the cooling of the motor ribs in order to avoid downtime and breakdown.
Companies that use STARK Forced Ventilation do so because of the following reasons:
- Overheating prevention
- Motor breakdown avoidance
- Works with all electric motors
- IP66 protection
- Extreme low noise levels
- Helping engineers with a compact and reliable solution
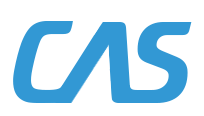
Compact Airflow System
The innovative Compact Airflow System (CAS) is developed to ensure high level performance in all types of environments. As result of the sophisticated design, characteristic curve and optimized heat dispersal STARK forced ventilation fans work very efficient.
Because of the slightly triangular intake, air can flow into the fan unit at a 90 degree angle. For instance when placed directly against a wall or flat surface. This makes STARK fans compact and very suitable for situations with limited space.

Highly Efficient Forced Ventilation
All ventilation units are specially manufactured according to customer´s demand to fit on each individual electric motor or gear motor. Thus, a simple mounting or replacement of the fan units is assured.
STARK SVE PREMIUM
STARK SVE is a premium cooling fan, internationally certified with high ingress protection (IP66). This protects the ventilation unit against powerful water jets and makes the fan suitable for use in dusty or humid environments.
Certification: CCC, CE, UL, CSA, EAC
Compact Airflow System: yes
IEC size: 63-355
Protection Class: IP66
Phase: 3-phase, single phase
Max. airflow capacity (m³/h): 9,200
Voltage range (V): 220-277, 200-303, 356-525 ,575, 660, 690
STARK SVB BASIC
With the STARK SVB forced ventilation industrial companies benefit from a cost-effective and reliable fan that is suitable for applications where basic cooling and motor breakdown prevention plays an important role.
Certification: CCC, CE, EAC
Compact Airflow System: no
IEC size: 63-560
Protection Class: IP55
Phase: 3-phase
Max. airflow capacity (m³/h): 8,000
Voltage range (V): standard 220-240, 380-420, 575, 660, 690

Professional Customization
Stark Forced Ventilation also produces customized and special Forced Ventilation systems.
STARK Forced Ventilation: High-quality fans at Competitive Pricing
STARK Forced Ventilation is the answer to the demand for reliable high performance forced ventilation that meets European standards and at the same time is available at a very favorable price at an extensive network of European distributors.
Fast Delivery
Safe Packaging
International Distribution
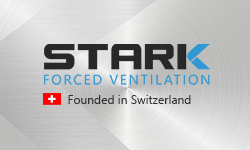
High quality forced ventilation at competitive pricing for companies that embrace the future of industry
Features STARK Forced Ventilation
- Worldwide stock and distribution
- Works with all electric motors
- Protection up to IP66
- CAS: Compact Airflow System
- Certificates CE, CURUS (UL and CSA), EAC
- Axial fans for optimized efficiency
- On average 30% more economical than other suppliers
- 2-year warranty
- Compact terminal box design
- Extreme low noise levels
- Ultra-high air volume flow
- Primed galvanized sheet for better corrosion prevention
Forced Ventilation Applications
Companies all over the world use STARK forced ventilation fans in applications such as:
machinery and equipment, compressors, shredders, presses, conveyor systems, metallurgy, chemical industry, medical equipment, steel- and paper industry
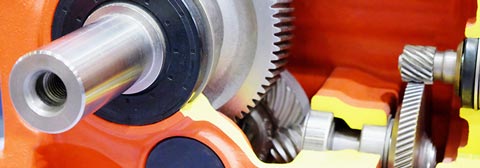
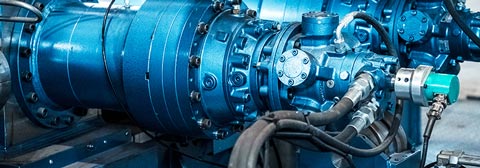
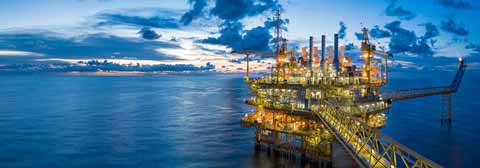
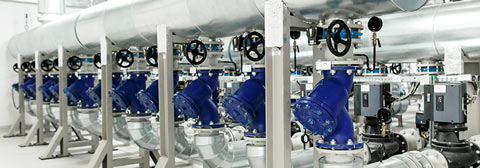
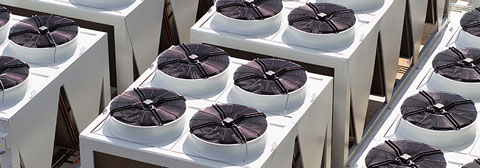
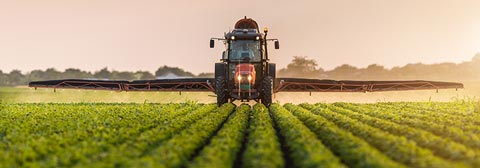
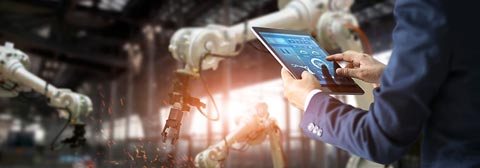
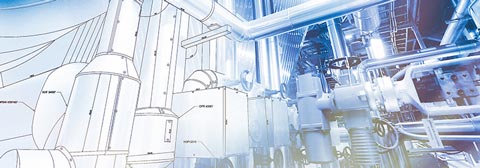
STARK and ABC Group
ABC Group is an innovation network of global partners that offers high quality industrial drive systems and components like STARK forced ventilation. By joining forces, ABC Group makes the way larger enterprises work available to smaller companies.
Central to this is international excellence, networks and growth. ABC Group is further characterized by:
- High quality in production, sales, service and maintenance
- Smart and cost efficient logistics organization
- Large stock with short delivery times thanks to the extensive global distribution network
- R&D, testing, prototyping and integration in drive systems
- Customer-specific electric motor and drive solutions
- Knowledge sharing and exchange of strategic information between all partners